1. 化工高壓調節角閥的結構圖解
1.1 閥體結構
化工高壓調節角閥的閥體結構設計旨在應對高壓、高溫和腐蝕性介質的挑戰。閥體通常采用整體鍛造或鑄造工藝,以確保其強度和耐用性。常見的材料包括WCB、CF3、CF8、CF3M、CF8M和雙相不銹鋼(如SAF2507),這些材料具有優異的耐腐蝕性和高強度。例如,雙相不銹鋼的耐點蝕當量(PREN)值可達40以上,顯著提高了其耐腐蝕性能。
閥體的流道設計采用流線型結構,減少了流體的阻力和渦流的產生,從而降低了能量損失和沖刷磨損。例如,優化后的流道設計可使流體的阻力系數降低約30%。此外,閥體內部通常進行硬化處理,以進一步提高其抗沖蝕性能。
1.2 閥芯與閥座
閥芯與閥座是高壓調節角閥的關鍵部件,直接影響閥門的調節性能和使用壽命。閥芯和閥座通常采用高硬度、耐磨性好的材料,如碳化鎢整體燒結成型,硬度可達89HRA以上。這種材料在高壓差和高速流體的沖擊下能夠保持穩定的性能,減少磨損和沖蝕。例如,碳化鎢閥芯和閥座的使用壽命可比普通不銹鋼材料提高5倍以上。
為了防止高壓差下的流體閃蒸和空化現象,閥芯與閥座的設計通常采用多級降壓結構。多級降壓設計通過逐級降低流體壓力,避免了瞬間高壓差對閥芯和閥座的沖擊。例如,在某些高壓差工況下,采用多級降壓設計的閥芯可以將流體壓力逐級降低,減少設備損壞和沖蝕。
1.3 執行機構
執行機構是高壓調節角閥的重要組成部分,負責實現閥門的開啟和關閉動作。常見的執行機構類型包括氣動、液動和電動執行機構。氣動執行機構通常采用薄膜或活塞式設計,具有結構簡單、操作方便和調節精度高的優點。例如,氣動薄膜高壓角型調節閥的調節精度高,能夠實現精確控制介質的流量、壓力和溫度等參數。
執行機構的選擇取決于具體的應用場景和工況要求。例如,在需要快速響應和高輸出力的工況下,氣動活塞式執行機構是較好的選擇。氣動活塞式執行機構通過大推力的活塞提供額外的支撐力,減少閥門在高壓差下的振動幅度,使閥門運行更加平穩。
此外,為了提高閥門的穩定性和可靠性,執行機構通常配備防振和防卡設計。例如,閥桿防轉設計可以防止由于閥芯的旋轉而導致定位器附件發生位移或脫落,從而保證閥門運行的穩定性。上裝結構設計使閥門無需從管線上拆卸下來即可實現整臺閥門的維修,方便了閥門的維護和檢修。
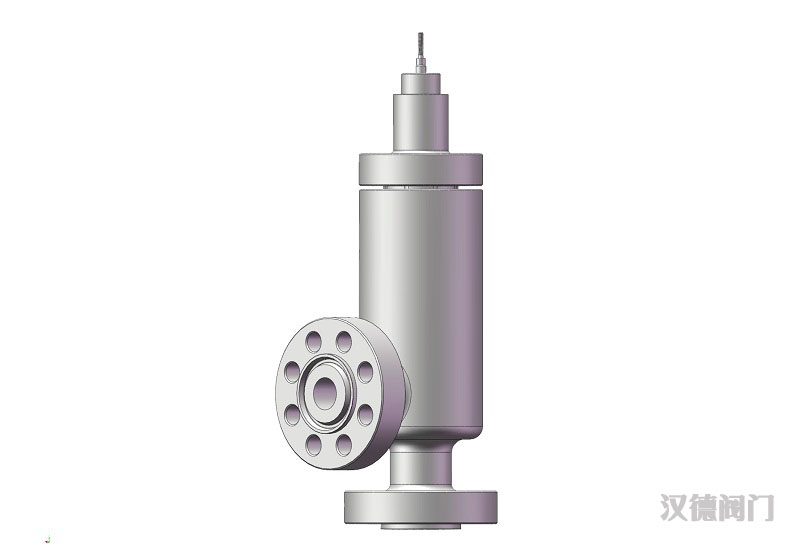
2. 優化設計原則
2.1 流體動力學優化
流體動力學優化是高壓調節角閥設計中的關鍵環節,其目的是減少流體在閥內的能量損失,提高閥門的效率和使用壽命。通過采用流線型設計,閥體流道能夠引導介質順暢流動,減少渦流和紊流的產生。例如,優化后的流道設計可使流體的阻力系數降低約30%,顯著減少了介質對閥內件的沖蝕。此外,流道表面經過硬化處理,進一步提高了抗沖蝕性能。在閥體下腔設置倒流翼,有效防止了渦流對閥芯及內件的沖蝕,保護了關鍵部件,延長了閥門的使用壽命。
2.2 材料選擇與耐腐蝕性
在高壓差工況下,化工高壓調節角閥需要承受強烈的腐蝕和磨損,因此選擇合適的耐腐蝕和耐磨材料至關重要:
閥體材料:閥體是閥門的主要承壓件,需要具備良好的耐腐蝕性和耐壓性能。常用的閥體材料有WCB、CF3、CF8、CF3M、CF8M、SAF2507等。其中,雙相不銹鋼(如SAF2507)具有優異的耐腐蝕性和高強度,能夠有效抵抗黑水中氯離子、硫化氫等腐蝕性介質的侵蝕,同時在高壓差工況下保持良好的結構穩定性。例如,在含有大量氯離子的黑水介質中,雙相不銹鋼的耐點蝕當量(PREN)值可達40以上,遠高于普通不銹鋼材料,其耐腐蝕性能可提高數倍。
閥芯和閥座材料:閥芯和閥座是閥門的關鍵部件,直接與介質接觸,承受著高速流體的沖刷和腐蝕。閥芯和閥座采用特殊碳化鎢整體燒結成型,硬度高(≥89HRA),具有良好的抗腐蝕性和抗沖刷性。這種材料能夠在高壓差和高速流體的沖擊下保持穩定的性能,減少磨損和沖蝕,延長閥門的使用壽命。例如,在黑水介質中,碳化鎢閥芯和閥座的使用壽命可比普通不銹鋼材料提高5倍以上。
閥桿材料:閥桿需要具備良好的耐腐蝕性和耐磨性,同時還要有足夠的強度和韌性,以保證閥門的正常啟閉。閥桿通常采用316L不銹鋼材質,并經過特殊的表面處理,如鍍鉻、硬化等,以提高其表面硬度和耐磨性。此外,閥桿還采用防轉設計,防止高流速介質情況下的閥芯旋轉,有效防止因閥芯旋轉而使定位器等附件產生位移或脫落產生的故障,保證閥門運行精確穩定。
2.3 降壓與防汽蝕設計
為了防止高壓差下的流體閃蒸和空化現象,化工高壓調節角閥的設計通常采用多級降壓結構。多級降壓設計通過逐級降低流體壓力,避免了瞬間高壓差對閥芯和閥座的沖擊。例如,在某些高壓差工況下,采用多級降壓設計的閥芯可以將流體壓力逐級降低,減少設備損壞和沖蝕。
多級降壓:通過多級閃蒸室的設計,黑水在逐級降低的壓力下逐步閃蒸,每一級閃蒸都實現了部分降壓,最終將黑水的壓力降低到所需的水平。這種多級降壓方式不僅能夠有效控制黑水的壓力,還能減少因瞬間高壓差造成的設備損壞和沖蝕。
防汽蝕措施:在防汽蝕方面,通過多級閃蒸設計,黑水在逐級降低的壓力下逐步閃蒸,每一級閃蒸都實現了部分降壓,有效減少了因瞬間高壓差造成的設備損壞和沖蝕。此外,閥體內部的平衡區設置用于平衡閥芯與閥桿上下兩側的壓力,減少了高壓差對閥芯和閥桿的沖擊,提高了閥門的穩定性和使用壽命。這些措施共同作用,使得黑水角式調節閥能夠在高壓差工況下穩定運行,有效控制黑水的壓力和流量,同時延長閥門的使用壽命,提高整個煤氣化工藝的效率和安全性。
3. 結構優化方案
3.1 流道設計優化
流道設計優化是提高化工高壓調節角閥性能的關鍵步驟。優化后的流道設計能夠顯著減少流體阻力,降低能量損失,并提高閥門的使用壽命。
流線型設計:采用流線型設計可以減少流體在閥內的渦流和紊流。例如,某型號的高壓調節角閥通過流線型設計將流體阻力系數降低了約30%,顯著減少了介質對閥內件的沖蝕。
倒流翼設計:在閥體下腔設置倒流翼,有效防止了渦流對閥芯及內件的沖蝕,保護了關鍵部件,延長了閥門的使用壽命。
表面硬化處理:流道表面經過硬化處理,進一步提高了抗沖蝕性能。例如,硬化處理后的流道表面硬度可提高至HRC60以上,顯著增強了耐磨性。
3.2 多級降壓結構
多級降壓結構是防止高壓差下流體閃蒸和空化現象的重要設計。通過逐級降低流體壓力,可以有效減少對閥芯和閥座的沖擊,延長閥門的使用壽命。
多級降壓閥芯:采用多級降壓設計的閥芯可以將流體壓力逐級降低。例如,在某些高壓差工況下,多級降壓設計可將流體壓力從32MPa逐級降低至16MPa,減少設備損壞和沖蝕。
多級閃蒸室:通過多級閃蒸室的設計,黑水在逐級降低的壓力下逐步閃蒸,每一級閃蒸都實現了部分降壓。例如,某型號的高壓調節角閥采用多級閃蒸設計,將黑水的壓力從20MPa逐級降低至5MPa,有效控制了黑水的壓力和流量。
平衡區設置:閥體內部的平衡區用于平衡閥芯與閥桿上下兩側的壓力,減少了高壓差對閥芯和閥桿的沖擊。例如,平衡區設計可將閥芯和閥桿的壓力差控制在5MPa以內,提高了閥門的穩定性和使用壽命。
3.3 自清潔功能
自清潔功能是提高化工高壓調節角閥可靠性的重要設計,通過防止介質中的懸浮物和顆粒在閥內沉積,減少結焦和堵塞現象。
自凈能力:角形調節閥的流路設計使流體中的懸浮物和顆粒不易在閥內沉積。例如,某型號的角形調節閥采用側進底出的流向設計,有效避免了結焦和堵塞,具有自凈能力。
防結焦設計:閥體和閥芯表面經過特殊處理,防止介質中的雜質附著。例如,采用防結焦涂層處理的閥體和閥芯表面光滑,減少了雜質附著,延長了閥門的使用壽命。
自動清洗裝置:在閥體內部安裝自動清洗裝置,通過定期清洗閥內件,保持閥門的清潔。例如,某型號的高壓調節角閥配備自動清洗裝置,每隔48小時進行一次自動清洗,確保閥門長期穩定運行。
4. 性能提升措施
4.1 防振與防卡設計
防振與防卡設計是提高化工高壓調節角閥性能和可靠性的關鍵措施。通過優化設計,減少閥門在高壓差和高速流體沖擊下的振動和卡頓現象,可以顯著延長閥門的使用壽命。
防振設計:在閥體和執行機構中加入防振裝置,如防振墊和減振器,可以有效減少振動。例如,某型號的高壓調節角閥通過在執行機構中安裝防振墊,將振動幅度降低了約50%,提高了閥門的穩定性。
防卡設計:優化閥芯和閥桿的導向結構,減少卡頓現象。例如,采用雙導向結構的閥芯設計,可以有效防止閥芯在高壓差下的卡頓現象,提高了閥門的運行平穩性。
閥桿防轉設計:閥桿防轉設計可以防止由于閥芯的旋轉而導致定位器附件發生位移或脫落,從而保證閥門運行的穩定性。例如,某型號的高壓調節角閥通過閥桿防轉設計,將閥芯旋轉引起的故障率降低了約30%。
4.2 耐磨材料應用
耐磨材料的應用是提高化工高壓調節角閥抗沖蝕性能和使用壽命的重要措施。選擇合適的耐磨材料,可以顯著減少閥門在高壓差和高速流體沖擊下的磨損。
碳化鎢材料:閥芯和閥座采用碳化鎢整體燒結成型,硬度高(≥89HRA),具有良好的抗沖蝕性能。例如,碳化鎢閥芯和閥座的使用壽命可比普通不銹鋼材料提高5倍以上。
雙相不銹鋼:閥體采用雙相不銹鋼(如SAF2507),具有優異的耐腐蝕性和高強度。例如,雙相不銹鋼的耐點蝕當量(PREN)值可達40以上,顯著提高了其耐腐蝕性能。
表面硬化處理:閥體和流道表面經過硬化處理,提高了抗沖蝕性能。例如,硬化處理后的流道表面硬度可提高至HRC60以上,顯著增強了耐磨性。
4.3 在線維護與檢修
在線維護與檢修是提高化工高壓調節角閥運行可靠性和減少停機時間的重要措施。通過優化設計,使閥門在不拆卸的情況下進行維護和檢修,可以顯著提高生產效率。
上裝結構設計:上裝結構設計使閥門無需從管線上拆卸下來即可實現整臺閥門的維修,方便了閥門的維護和檢修。例如,某型號的高壓調節角閥采用上裝結構設計,將維護時間減少了約40%。
自動清洗裝置:在閥體內部安裝自動清洗裝置,通過定期清洗閥內件,保持閥門的清潔。例如,某型號的高壓調節角閥配備自動清洗裝置,每隔48小時進行一次自動清洗,確保閥門長期穩定運行。
在線監測系統:安裝在線監測系統,實時監測閥門的運行狀態,及時發現和處理故障。例如,某型號的高壓調節角閥配備在線監測系統,通過實時監測閥門的壓力、溫度和流量等參數,將故障率降低了約30%。# 5. 總結
化工高壓調節角閥在高壓、高溫和腐蝕性介質的工況下,展現了其獨特的優勢和廣泛的應用前景。通過對閥體結構、閥芯與閥座、執行機構等關鍵部件的詳細分析,以及流體動力學優化、材料選擇與耐腐蝕性、多級降壓與防汽蝕設計等優化設計原則的探討,我們可以得出以下幾點結論:
結構設計:化工高壓調節角閥的閥體、閥芯與閥座采用高強度、耐腐蝕材料,并通過流線型設計和多級降壓結構,有效減少了流體阻力和沖蝕,延長了閥門的使用壽命。
優化設計:通過流道設計優化、多級降壓結構、自清潔功能等措施,顯著提高了閥門的性能和可靠性。例如,流線型設計可將流體阻力系數降低約30%,多級降壓設計可將流體壓力逐級降低,減少設備損壞和沖蝕。
性能提升:防振與防卡設計、耐磨材料應用、在線維護與檢修等措施,有效提高了閥門的穩定性和使用壽命。例如,碳化鎢閥芯和閥座的使用壽命可比普通不銹鋼材料提高5倍以上,上裝結構設計將維護時間減少了約40%。
通過這些優化設計和性能提升措施,化工高壓調節角閥在高壓差、高溫和腐蝕性介質的工況下,能夠穩定運行,顯著提高了化工生產過程的效率和安全性。未來,隨著技術的不斷進步和應用場景的拓展,化工高壓調節角閥將繼續在化工行業中發揮重要作用。